PD5010 Milk Reception System
In 1988 Specialty Process Systems Ltd. designed and installed the first Measurement Canada approved PD3010 Milk Reception System here in Winnipeg, Manitoba under Measurement Canada approval SWA-2176. To the present, we have sold and continue to service an installed base from Coast to Coast in Canada and the United States.
Todays Dairy business demands accountability for quality control, shrinkage due to lost product & information management. The system uses many of the same operating principles that were introduced in the PD3010 system. The main operating component of either the PD3010 or PD5010 milk reception system is the PD340X flow transmitter, which offers unprecedented accuracy and repeatability when installed correctly as a part of the approved milk reception system. The system incorporates an automatic composite sampling device that will allow sampling policy selectable sample draw and bottle sizes, which comply with local milk governing bodies. Temperature is also incorporated into the function of the controller and will stop the system to require an operator acknowledgement prior to continuing with the unloading of milk if the raw product temperature exceeds the maximum allowed temperature, thus ensuring incoming milk is received within the processors tolerances for quality. The vacuum air eliminator ensures that only the product to be measured registers on the PD340X. The micro processor will monitor the system for any possible errors during measurement and will shut the system down if a critical error occurs. Any errors present during measurement are included on the print out at the end of each delivery. After each delivery, the data collected by the system "transporter number, route number, manifest volume, actual volume, difference in %, temperature" can either be printed locally on a roll printer or stored and down loaded for use on a local PC.
The user friendly operator interface allows simple entry of manifest derived information. The operator will key in transport number, route number and pick up volume and simply press start. The inlet valve will open allowing product into the vacuum air eliminator and the air relief valve will open allowing air to exhaust from the vacuum air eliminator. As the product enters the air eliminator the product will follow the contour of the vacuum air eliminator creating a vortex which allows the air to be pulled out of the milk and drawn to the centre. Once the high level in the air eliminator is reached, the air relief valve closes and the pump starts. The vacuum air eliminator is now in a vacuum state, which further enhances its ability to draw air out of the product and into the centre of the vortex. The product will continue to be drawn into the air eliminator under vacuum until such a time that all of the product from the tanker truck has been delivered. As the final product from the tanker drains into the vacuum air eliminator the level in the vacuum air eliminator will drop to medium level at which point the flow control valve will reduce the flow of the system and the air relief valve will open breaking the vacuum in the air eliminator and venting to atmosphere. Finally the system will empty to low level (prime volume) and the measurement will be stopped and can now printed. **Prime volume is the volume of liquid left after each delivery. It is equal to the volume of product in the vacuum air eliminator between the low level and the PD340X flow transmitter (this volume is accounted for on the first delivery of each day).
Since its inception in 1988 the PD3010 has been superseded by the PD5010 Milk Reception System. The main differences between the systems are the PD5010 offers twice the processing power of the PD3010, the PD5010 stores its program in flash memory versus the old eprom technology used in the PD3010 which means a program modification can easily be made online without the need for swapping out eproms. The PD5010 also utilizes a field replaceable battery.
H.T.S.T. & Pasteurizing Systems
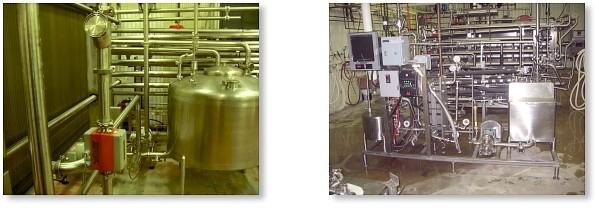
Specialty Process System Ltd. has the understanding and ability to design and fabricate pasteurizing systems tailored specifically to the customers needs while complying with and conforming to local and CFIA regulations. We have been involved in and have experience with minor projects where modifications to HTST capacity or upgrades and improvements to control may be required and are also capable of designing and building H.T.S.T. systems and PLC based control to suit a larger scale turn key installation. We have successfully designed and modified many HTST systems locally including many custom manufactured heating and cooling skids to suit a customers particular process needs.
We also distribute stand alone components that will enhance your HTST process:
- Hot Water Sets & Controls
- HTST Recorder/Controllers
- Meter Based Timing
- HTST valves
- CPM & Backpressure Valves
- C.I.P. able Vacuum Breakers
- RTDs
- Differential Pressure Control
- Indicating Thermometers
- Timing - Booster -Stuffing Pumps
- Optical Sensors
- Balance Tank Level Control
- Balance / Constant Level Tanks
- Plate and frame heat exchangers/shell and tube heat exchangers
C.I.P. Systems
From single use skid mounted CIP systems that may be used in a Beverage plant to multi-tank re-use systems that may be used in a Dairy plant our experience designing and supplying Clean in Place systems will allow us to provide a solution to suit the customers requirements. PLC based control with data collection and capture are also available as insurance that specific Time, Temperature, Flow and Conductivity requirements are being met.
We also distribute stand alone components that will enhance your C.I.P. process:
- Conductivity Sensors
- RTDs
- Circular Chart Recorders
- Pressure Transmitters
- Flow Metering Devices
- Supply & Return Pumps
- Flow Switches
- Optical Sensors
- C.I.P. Tanks
- Plate and frame heat exchangers/shell and tub heat exchangers